Imperfect Shape and Dimensions according to BS EN ISO 6520-1
Types of Imperfect Shapes and Dimensions:
- Undercut
- Melting of top edge due to high welding current (especially at the free edge) or high travel speed Prevention: Reduce power input, especially approaching a free edge where overheating can occur
- Attempting a fillet weld in horizontal-vertical (PB) position with leg length >9mm Prevention: Weld in the flat position or use multi-run techniques
- Excessive/incorrect weaving Prevention: Reduce weaving width or switch to multiruns
- Incorrect electrode angle Prevention: Direct arc towards thicker member
- Incorrect shielding gas selection (MAG) Prevention: Ensure correct gas mixture for material type and thickness (MAG)
- Excess weld metal
- Excess arc energy (MAG, SAW) Prevention: Reduction of heat input
- Shallow edge preparation Prevention: Deepen edge preparation
- Faulty electrode manipulation or build-up sequence Prevention: Improve welder skill
- Incorrect electrode size Prevention: Reduce electrode size
- Travel speed too slow Prevention: Ensure correct travel speed is used
- Incorrect electrode angle Prevention: Ensure correct electrode angle is used
- Wrong polarity used (electrode polarity DC-ve (MMA, SAW) Prevention: Ensure correct polarity ie DC+ve Note DC-ve must be used for TIG
- Excess penetration
- Weld heat input too high Prevention: Reduce arc voltage and/or welding current;increase welding speed
- Incorrect weld preparation ie excessive root gap, thin edge preparation, lack of backing Prevention: Improve workpiece preparation
- Use of electrode unsuited to welding position Prevention: Use correct electrode for position
- Lack of welder skill Prevention: Retrain welder
- Overlap
- Poor electrode manipulation (MMA) Prevention: Retrain welder
- High heat input/low travel speed causing surface flow of fillet welds Prevention: Reduce heat input or limit leg size to 9mm maximum for single pass fillets
- Incorrect positioning of weld Prevention: Change to flat position
- Wrong electrode coating type resulting in too high a fluidity Prevention: Change electrode coating type to a more suitable fast freezing type which is less fluid
- Linear misalignment
- Inaccuracies in assembly procedures or distortion from other welds Prevention: Adequate checking of alignment prior to welding coupled with the use of clamps and wedges
- Excessive out of flatness in hot rolled plates or sections Prevention: Check accuracy of rolled section prior to welding
- Angular distortion
- Incompletely filled groove
- Insufficient weld metal Prevention: Increase the number of weld runs
- Irregular weld bead surface Prevention: Retrain welder
- Irregular width
- Severe arc blow Prevention: Switch from DC to AC, keep arc length as short as possible
- Irregular weld bead surface Prevention: Retrain welder
- Root concavity
- Insufficient arc power to produce positive bead Prevention: Raise arc energy
- Incorrect preparation/fit-up Prevention: Work to WPS
- Excessive backing gas pressure (TIG) Prevention: Reduce gas pressure
- Lack of welder skill Prevention: Retrain welder
- Slag flooding in backing bar groove Prevention: Tilt work to prevent slag flooding
- Burn-through
- Insufficient travel speed Prevention: Increase the travel speed
- Excessive welding current Prevention: Reduce welding current
- Lack of welder skill Prevention: Retrain welder
- Excessive grinding of root face Prevention: More care taken, retrain welder
- Excessive root gap Prevention: Ensure correct fit-up

An irregular groove at the toe of a run in the parent metal or previously deposited weld metal due to welding. Characterised by its depth, length and sharpness.
Causes:

Excess weld metal is the extra metal that produces excessive convexity in fillet welds and a weld thickness greater than the parent metal plate in butt welds. It is regarded as an imperfection only when the height of the excess weld metal is greater than a specified limit.
Causes:

Projection of the root penetration bead beyond a specified limit, local or continuous.
Causes:

Imperfection at the toe of a weld caused by metal flowing on to the surface of the parent metal without fusing to it.
Causes:
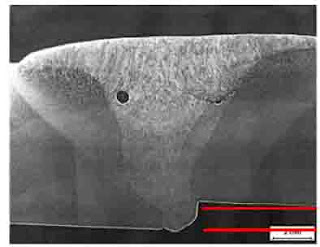
Misalignment between two welded pieces such that while their surface planes are parallel, they are not in the required same plane.
Causes:

Misalignment between two welded pieces such that their surface planes are not parallel or at the intended angle. Causes and prevention are the same as for linear misalignment.

Continuous or intermittent channel in the weld surface due to insufficient deposition of weld filler metal.
Causes:

Excessive variation in width of the weld.
Causes:

A shallow groove that occurs due to shrinkage at the root of a butt weld.
Causes:

A collapse of the weld pool resulting in a hole in the weld.
Causes:
Imperfect Shape and Dimensions according to BS EN ISO 6520-1
Reviewed by belajar koor
on
4:11 AM
Rating:

No comments: